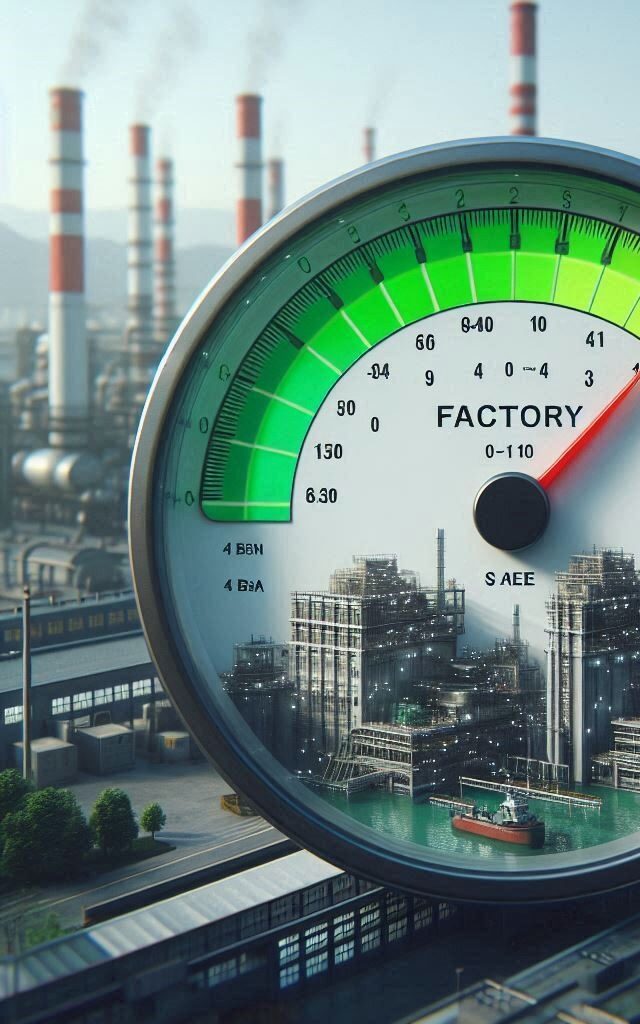
Compressed air is one of the most common ways to power actuators in machines and production lines. Its versatility and reliability make it indispensable in many industries. Nevertheless, the compressed air preparation process is quite energy–intensive, which can lead to significant operating costs. In this article, we want to show you what to look for when using this energy carrier and how you can increase its efficiency to get the most out of your compressed air while reducing your expenses and environmental impact.
How compressed air is generated
How to build a compressed air supply system
Air-saving opportunities – in mechanical engineering
A key way to save compressed air is to reduce the operating pressure from the 6 bar level commonly used in factories in Europe to 4 bar. An example of the effective use of this approach are Japanese companies that have been using reduced pressure in their pneumatic systems for years. Pressure relief is particularly possible and beneficial when building new production lines and machines.
Our company, during the design of devices, pays special attention to subsequent operating costs. This requires designing the pneumatic system and actuators in such a way that they can operate efficiently at reduced pressure. By using lower pressure, components selected during the design phase have a longer service life. The seals on the pistons of the cylinders wear less, and the entire air preparation system retains its functionality for longer.
Reducing the pressure not only increases the life of the components, but also significantly reduces operating costs. Lower operating pressure means less energy is used to compress air, which directly translates into cost savings and reduced CO2 emissions.
The use of a depressurization strategy in compressed air systems is therefore both economically and ecologically viable. Implementing this method when designing new production lines and machines is an investment in long–term efficiency and reliability, which is a priority in the modern approach to energy resource management in industry.