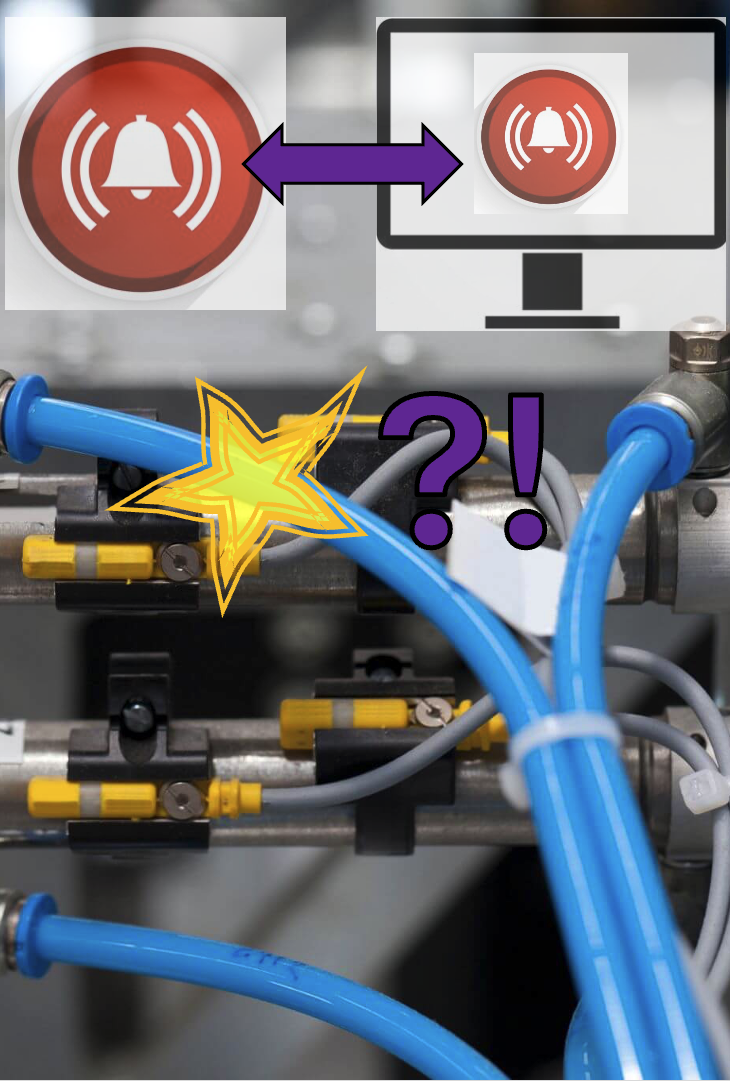
Diagnostyka układów pneumatycznych jest kluczowym elementem utrzymania ruchu w przemyśle, szczególnie w kontekście maszyn i urządzeń.
Kluczowe dla zachowania równowagi w działaniu linii produkcyjnej jest monitorowanie stanu urządzeń zainstalowanych w fabryce pod katem zażycia energii. W tym artykule skupimy się na monitorowaniu stanu układu pneumatycznego. Zachęcamy do zapoznania się z:
Zużycie powietrza – ponadnormatywne
Jest jednym z nagminnie spotykanych przez nas podczas audytów. (Analiza rentowności)
W większości przeprowadzonych przez nas analiz, Klienci (ich zespoły odpowiedzialne za stan maszyn i urządzeń na liniach produkcyjnych) nie zwracają uwagi, na tak prozaiczne rzeczy jak nieszczelności przewodów pneumatycznych czy elementów wykonawczych.
Utrzymanie ruch zazwyczaj (w natłoku bieżącego dbania o stan linii i rozwiązywania doraźnych problemów) nie ma czasu by poświęcić uwagę na tak „błahe” rzeczy jak nieszczelność. Ważne jest by linii „jechała”, a koszty? To drugorzędna sprawa.
Nad problemem nieszczelności skupiają się w momencie, gdy dany moduł maszyny działa nieprawidłowo i w wyniku braku wystarczającego przepływu:
- siłownik nie wysuwa się do końca,
- nie może podnieść danego modułu
lub
- wysuwa się w zbyt długim czasie.
Jak zapobiegać – monitoring w czasie rzeczywistym
W erze dynamicznego rozwoju przemysłu 4.0, a obecnie przemysłu 5.0, producenci maszyn, tacy jak my, kładą coraz większy nacisk na efektywne zarządzanie mediami oraz monitorowanie stanu technicznego maszyn. W naszych systemach, wykorzystujących sztuczną inteligencję (AI), monitorujemy szereg parametrów i porównujemy je w czasie rzeczywistym z wzorcem pracy maszyny, który został wyuczony na podstawie optymalnych warunków. Każda anomalia jest natychmiast wykrywana i rejestrowana, a powtarzające się błędy są raportowane, co zapobiega ich zignorowaniu.
W modułach linii produkcyjnych montujemy czujniki przepływu powietrza, które monitorują niekontrolowane straty powietrza. Taka konstrukcja układu pneumatycznego pozwala na szybkie odcięcie modułów maszyny narażonych na uszkodzenia (których nie dało się całkowicie osłonić lub zabudować) przez system AI, który informuje o awarii i wskazuje miejsce jej wystąpienia. Szybkość diagnostyki jest kluczowa, zwłaszcza przy pełnym obciążeniu linii produkcyjnej.
Dzięki zaawansowanym rozwiązaniom technologicznym, w przypadku wykrycia mikronieszczelności w układzie pneumatycznym, jesteśmy w stanie określić dobowy ubytek powietrza dla całej maszyny oraz oszacować straty wynikające z takiego stanu rzeczy.
Monitoring wyspy zaworowej
Inteligentne rozwiązania w dobrze zaprogramowanej maszynie umożliwiają samodiagnostykę stanu zaworów w wyspie zaworowej, co jest kluczowe dla zapewnienia niezawodności i wydajności całego układu pneumatycznego. Systemy te są w stanie stale monitorować stan logiczny, w jakim znajduje się każdy zawór, oraz analizować jego działanie w czasie rzeczywistym. Dzięki temu mamy pełną kontrolę nad takimi parametrami jak czas otwarcia zaworu — czy nie jest on zbyt długi — oraz upewniamy się, czy zawór prawidłowo się zamyka i czy nie występują na nim nieszczelności.
Monitorowanie, w czasie rzeczywistym, tych parametrów pozwala na natychmiastowe wykrywanie problemów, takich jak zużycie zaworu lub obecność zanieczyszczeń. Zanieczyszczenia te mogą wynikać z niewłaściwego przygotowania powietrza lub przedostania się niepożądanych cząstek do zaworu w inny sposób. Dzięki samodiagnostyce możliwe jest szybkie zidentyfikowanie takich problemów, co pozwala na podjęcie odpowiednich działań serwisowych przed wystąpieniem poważniejszych awarii. Tym samym, zaawansowane systemy monitoringu nie tylko podnoszą niezawodność maszyn, ale także optymalizują koszty utrzymania poprzez minimalizowanie przestojów i zapobieganie uszkodzeniom komponentów.
Zredukowany jest także czas jaki Utrzymanie ruchu musi spędzić, by zdiagnozować problem.
Monitoring stacji przygotowani powietrza
Monitoring stacji przygotowania powietrza jest kluczowym elementem zapewniającym bezpieczeństwo oraz niezawodność działania układów pneumatycznych w maszynach. W naszych rozwiązaniach stosujemy zarówno lokalne odcięcie powietrza dla konkretnego modułu maszyny, jak i globalne odcięcie całej maszyny. Taka dwuetapowa kontrola zapewnia pełne bezpieczeństwo pracy oraz ochronę przed ewentualnymi uszkodzeniami wynikającymi z niekontrolowanego przepływu powietrza.
Stacje przygotowania powietrza są wyposażone w czujniki przepływu powietrza, które monitorują zarówno jego zużycie, jak i obecność ciśnienia w systemie. Dzięki temu mamy 100% pewności, że w maszynie nie znajduje się niekontrolowane powietrze, co jest kluczowe dla bezpiecznego serwisowania i pracy maszyny. W przypadku nagłych, niespodziewanych spadków ciśnienia system jest w stanie automatycznie odciąć dopływ powietrza, co zapobiega potencjalnym uszkodzeniom, takim jak niekontrolowany ruch urwanego przewodu, który mógłby prowadzić do poważnych awarii.
Dla zapewnienia najwyższej jakości powietrza, stacje przygotowania powietrza na maszynie są wyposażone w czujniki automatycznego spustu kondensatu, który może pojawić się na wejściu maszyny. Jest to niezbędne, aby zapobiec gromadzeniu się nadmiernej ilości wody, która, jeśli nie zostanie usunięta, może dostać się do układu pneumatycznego maszyny. Woda w systemie pneumatycznym może powodować korozję elementów wykonawczych, co prowadzi do ogromnych kosztów serwisowych i przestojów produkcji. Dzięki zaawansowanemu monitorowaniu stacji przygotowania powietrza możliwe jest zatem nie tylko zwiększenie bezpieczeństwa, ale także optymalizacja kosztów utrzymania maszyny.
Podsumowanie
Podsumowując, diagnostyka układu pneumatycznego maszyn jest niezwykle istotnym elementem skutecznego utrzymania ruchu w przemyśle, szczególnie w kontekście dbałości o ciągłość produkcji i optymalizację kosztów. Efektywne monitorowanie zużycia powietrza oraz stanu technicznego poszczególnych komponentów pneumatycznych pozwala na szybkie wykrywanie anomalii i zapobieganie potencjalnym awariom, które mogą prowadzić do kosztownych przestojów.
Zastosowanie nowoczesnych technologii, takich jak sztuczna inteligencja (AI) do monitorowania parametrów w czasie rzeczywistym, umożliwia proaktywne podejście do konserwacji maszyn. Systemy te wykrywają nawet najdrobniejsze nieprawidłowości, takie jak mikronieszczelności czy zużycie zaworów, i dostarczają precyzyjnych informacji pozwalających na szybkie i skuteczne działanie serwisowe. Dodatkowo, wyposażenie stacji przygotowania powietrza w czujniki przepływu i automatyczne systemy spustu kondensatu, pozwala na utrzymanie najwyższej jakości powietrza w układzie pneumatycznym, co znacząco redukuje ryzyko korozji i innych uszkodzeń komponentów.
W dobie przemysłu 5.0, podejście oparte na predykcyjnej konserwacji (predictive maintenance) i zautomatyzowanej diagnostyce jest kluczem do podniesienia efektywności i rentowności zakładów produkcyjnych. Dlatego też tak ważne jest, aby zespół odpowiedzialny za utrzymanie ruchu był świadomy roli, jaką odgrywa precyzyjne monitorowanie układów pneumatycznych oraz dbał o bieżącą diagnostykę, minimalizując ryzyko przestojów i kosztów serwisowych.