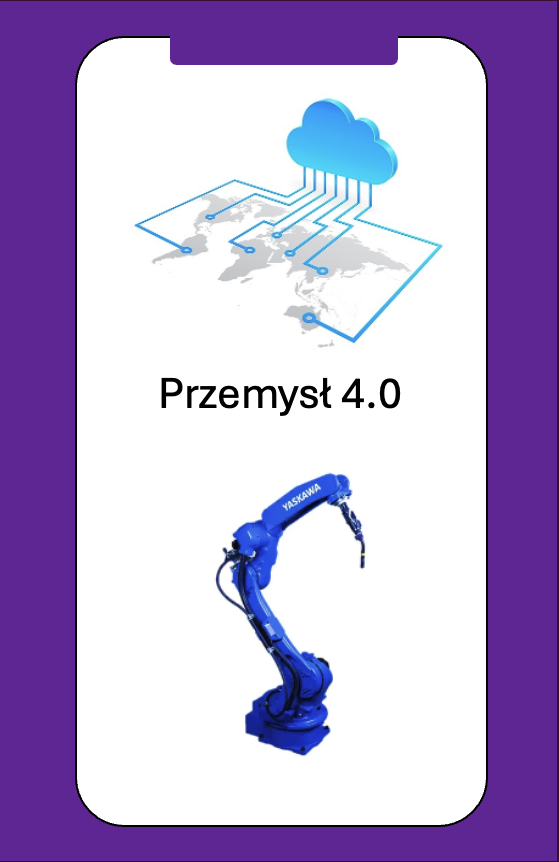
Historical outline
The first industrial revolution, which took place in the 18th century, introduced mechanization through the invention of the steam engine. The shift from manual labor to steam-powered machines significantly increased productivity and enabled mass production.
The second industrial revolution, at the turn of the 19th and 20th centuries, brought electrification and the development of assembly lines, further enhancing efficiency and enabling production on an even larger scale. The invention of the electric motor and the use of assembly lines revolutionized industries, allowing faster and more organized manufacturing processes.
The third industrial revolution, starting in the mid-20th century, introduced automation through electronics, information technology, and computers. The advent of programmable machines and robots enabled further automation and precision in production, as well as the development of more complex and advanced manufacturing systems.
Industry 4.0 builds upon and expands these earlier stages by integrating digital technologies, the Internet of Things (IoT), artificial intelligence (AI), and big data analytics to create intelligent, automated, and highly efficient manufacturing systems.
What is Industry 4.0
Industry 4.0 is a concept that revolutionizes the way industries operate by integrating advanced information and communication technologies into manufacturing processes. The main principles of Industry 4.0 include automation, robotics, the Internet of Things (IoT), artificial intelligence (AI), and big data analytics. All these elements aim to increase the efficiency, flexibility, and productivity of manufacturing processes.
Automation in the context of Industry 4.0 involves implementing advanced systems capable of performing repetitive tasks with high precision and reliability. Examples include industrial robots, automated production lines, and real-time production monitoring and management systems. Automation allows for the replacement of humans in tasks that are routine and easily automated. As a result, employees can be shifted to more creative and intellectually demanding tasks that require human intellect and creativity. Introducing new technologies requires employees to acquire new skills, particularly in areas related to operating and managing advanced technological systems. Automation can also enhance workplace safety and comfort by eliminating hazardous or monotonous tasks.
Labor market regulations (the next step in Industry 5.0)
Government regulations, such as the introduction of solidarity taxes, minimum wage laws, and a 4-day workweek, can also compel businesses to adopt automation. Solidarity taxes may increase labor costs, motivating companies to seek savings through automation and robotics. Rising minimum wages force enterprises to manage human resources more efficiently and may encourage investment in technologies that reduce operational costs. Shortening the workweek could necessitate increased production efficiency, achievable through process automation.
Summary
Industry 4.0, through automation and robotics, creates opportunities for more efficient management of human and technological resources. Government regulations can further accelerate this process by encouraging companies to invest in new technologies. Employees freed from monotonous tasks can focus on more creative and complex aspects of work, ultimately contributing to overall productivity and innovation.