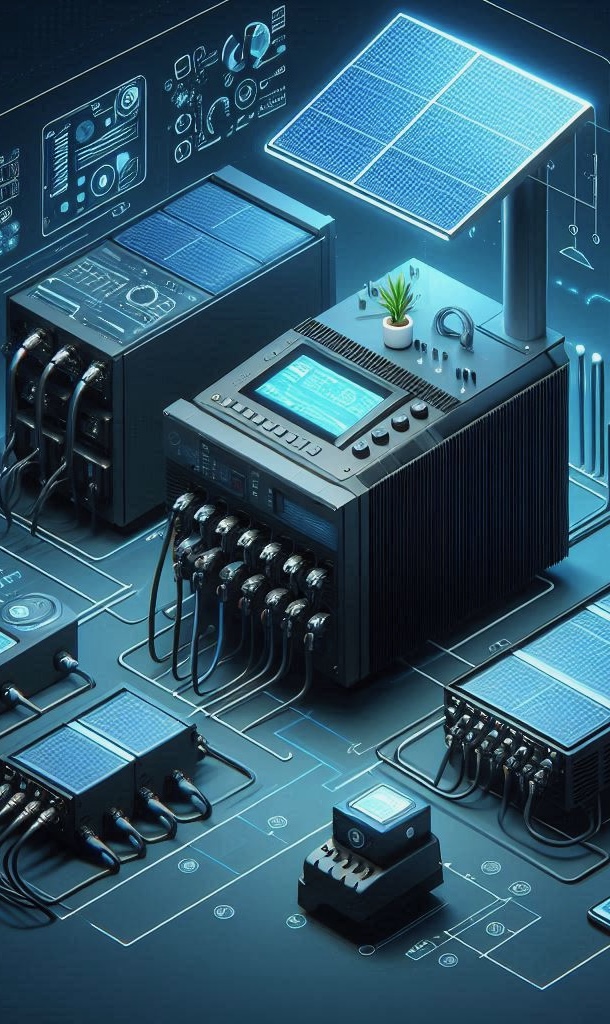
In today’s world, manufacturing plants face the challenge of efficiently managing energy consumption. Electric drives constitute a significant portion of total energy consumption, which is a crucial factor impacting operational costs. In light of rising energy prices and environmental protection requirements, manufacturers are compelled to seek innovative solutions that enable energy savings. Inverters with an energy feedback function to the grid are emerging as a response to these needs, offering technical possibilities for optimizing energy use in electric drives.
Problem
Traditional drives with AC motors have several significant drawbacks affecting their energy efficiency. First and foremost, they consume a large amount of energy during stopping and starting processes. These processes are not only energy-intensive but also cause increased mechanical wear, shortening the lifespan of devices and increasing operating costs.
In manufacturing plants where drives must frequently stop and start, these problems are particularly pronounced. Each start and stop generates energy losses, which accumulate over the year, resulting in significant operational costs.
Solution
Inverters, also known as frequency converters, provide an effective solution to these problems. With the ability to precisely control motor speed, inverters allow for the optimization of energy consumption in electric drives. By using start and stop speed ramps, they eliminate issues associated with frequent stopping and starting, enabling dynamic speed adjustments to match current demand.
A key advantage of modern inverters is the energy feedback function to the grid. During braking, kinetic energy, which would be lost as heat in traditional systems, is recovered and directed back to the power grid or shared with other inverters in the system.
Effects
Inverters with an energy feedback function to the grid offer numerous benefits, both economically and environmentally:
- Energy Savings: By recovering energy during braking, manufacturing plants can significantly reduce their energy consumption.
- Reduced Operating Costs: Lower energy consumption directly translates to lower electricity bills.
- Reduced Mechanical Wear: Eliminating frequent stops and starts reduces mechanical wear on drives, extending their lifespan and lowering maintenance costs.
- Environmental Impact: Reduced energy consumption and more efficient resource management contribute to a smaller carbon footprint for the manufacturing plant.
Implementation of Solutions
Implementing inverters with an energy feedback function to the grid in manufacturing plants can significantly enhance energy efficiency and reduce negative environmental impacts. Machine manufacturers focusing on long-term economic use should emphasize educating customers about the carbon footprint and its impact on business profitability.
Reactive power generated by electrical devices significantly affects energy consumption in manufacturing plants. Modern inverter solutions with an energy feedback function “monitor” the introduction of energy into the grid in the least disruptive way. Unlike systems based on braking resistors, which offer no ecological or economic benefits, inverters with an energy feedback function provide a more sustainable solution by minimizing energy waste and supporting sustainable development.
Conclusion
Inverters with an energy feedback function to the grid are a modern technical solution that allows for efficient energy management in electric drives. They enable significant energy savings, cost reductions, and reduced environmental impact. Introducing such technologies in manufacturing plants is a step towards sustainable development and long-term economic efficiency.