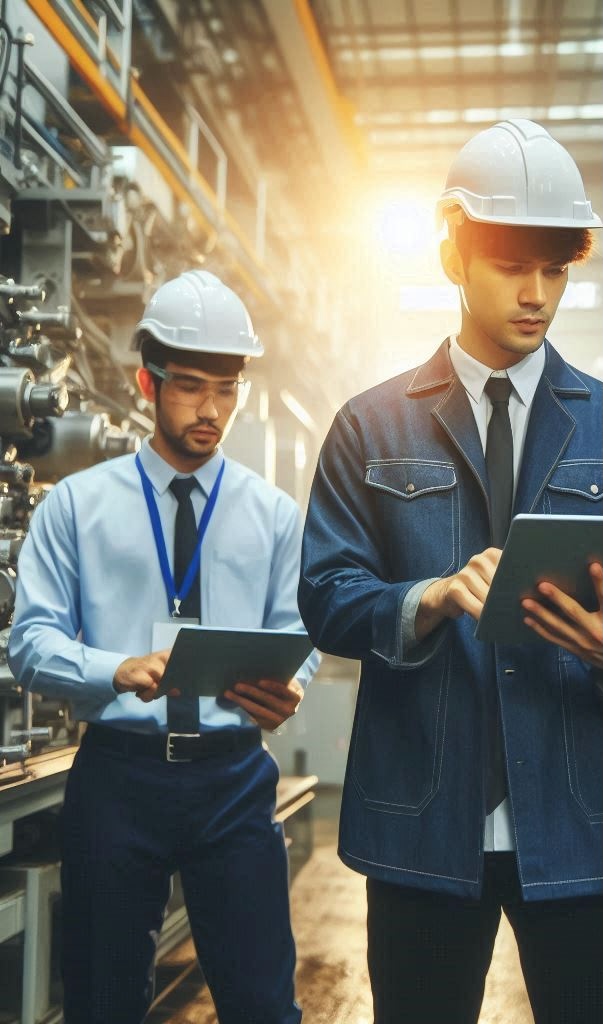
W dzisiejszych czasach, w erze Przemysłu 4.0, innowacje w zakresie monitorowania stanu maszyn rewolucjonizują sposób, w jaki funkcjonuje przemysł.
W dobie szybkiego postępu technologicznego, przemysł znajduje się na skraju wielkiej transformacji. Przemysł 4.0, znany również jako czwarta rewolucja przemysłowa, wprowadza zaawansowane technologie, które znacząco zmieniają tradycyjne metody monitorowania stanu maszyn. Innowacyjne podejście do monitorowania pozwala na efektywne zarządzanie i konserwację maszyn, eliminując konieczność stosowania licznych czujników takich jak oscyloskopy czy tensometry.
Tradycyjne metody a nowoczesne technologie
Nasza firma, dzięki bogatemu doświadczeniu w tradycyjnym podejściu do monitorowania maszyn, jest doskonale zaznajomiona z zaletami i wadami obu rozwiązań. Tradycyjne metody, które opierają się na licznych czujnikach do pomiaru drgań, siły tarcia czy momentu, wymagają rozbudowanego systemu sterowania oraz są kosztowne i skomplikowane w implementacji. W odpowiedzi na te wyzwania, łączymy tradycyjne podejście tam, gdzie jest to niezbędne, z nowoczesnym podejściem do predictive maintenance, czyli wyprzedzających działań konserwacyjnych.
Korzyści z redukcji ilości użytego sprzętu
Redukcja ilości czujników na maszynie przynosi liczne korzyści. Obniżenie kosztów początkowej implementacji jest jednym z kluczowych aspektów. Mniejsza liczba czujników to mniejsze wydatki na ich zakup, okablowanie oraz integrację w systemie sterowania. Ponadto, zmniejszenie liczby komponentów oznacza mniej potencjalnych punktów awarii. Jest to szczególnie istotne w przemyśle ciężkim, takim jak prefabrykacja przemysłowa czy produkcja zbrojeń stalowych.
Nowoczesne podejście do monitorowania stanu maszyn
W nowoczesnych systemach monitorowania stanu maszyn wykorzystuje się zaawansowane technologie automatyzacji. Serwonapędy z monitorowaniem momentu i ilości obrotów stają się standardem, jednak nawet zwykłe napędy elektryczne mogą dostarczać wartościowych danych do analizy. Dzięki agregacji danych z napędów możliwe jest tworzenie precyzyjnych modeli zużycia maszyn, co pozwala na prognozowanie ich stanu.
Analiza danych i optymalizacja procesów
Analiza danych zebranych z produkcji umożliwia prognozowanie stopnia zużycia oraz identyfikację komponentów wymagających konserwacji. Klient zyskuje możliwość monitorowania pracy operatorów, co wspiera optymalizację procesów produkcyjnych. Działania oparte na analizie danych pozwalają na planowanie konserwacji oraz wymiany komponentów w odpowiednich momentach, co znacząco redukuje koszty eksploatacji i minimalizuje ryzyko nagłych awarii.
Przykłady zastosowania zaawansowanych technologii
Na liniach produkcyjnych znajduje ona szerokie zastosowanie, pozwalając na minimalizowanie przestojów i optymalizację procesów produkcyjnych.
W praktyce, na oprawach łożysk stosuje się często oscyloskopy do badania drgań wałów. Wibracje są jednym z kluczowych wskaźników zużycia łożysk, a ich dokładna analiza pozwala na przewidywanie momentu wymiany tych elementów. Alternatywnie, można stosować modelowanie zużycia na podstawie danych prądowych pobieranych z silników. Zbierając dane o prądzie pobieranym przez silnik, można analizować wzorce zużycia i przewidywać potencjalne awarie.
Kolejnym przykładem jest monitorowanie temperatury silnika w trakcie jego pracy. Czujniki temperatury mogą rejestrować nagrzewanie się silnika i odchylenia od normy, co na podstawie zebranych wcześniej danych pozwala na wykrycie potencjalnych problemów. Gdy temperatura przekracza ustalone granice, system predykcyjny może wydać ostrzeżenie o możliwej awarii.
Inne zastosowania obejmują monitorowanie ciśnienia w systemach hydraulicznych, gdzie czujniki ciśnienia mogą wykrywać odchylenia od normy i wskazywać na problemy z pompami lub przewodami. Czujniki ultradźwiękowe mogą być używane do wykrywania wycieków w instalacjach pneumatycznych, co pozwala na szybkie usunięcie problemu zanim wpłynie on na cały proces produkcyjny. Ponadto, instalowane stacje przygotowania powietrza (wymagane na każdej maszynie i linii technologicznej), mogą być wyposażone w czujniki przepływu powietrza, na podstawie których można monitorować ponadnormatywne zużycie powietrza na linii produkcyjnej, świadczące o nieszczelnościach. W dłuższej perspektywie może to nieść za sobą duże koszty pochłanianej energii przez sprężarki.
Wszystkie te przykłady pokazują, jak zastosowanie predykcyjnej konserwacji na liniach produkcyjnych pozwala na znaczące zwiększenie efektywności i niezawodności maszyn, redukując jednocześnie koszty utrzymania i przestoje.
Wpływ na efektywność i zrównoważony rozwój
Zaawansowane monitorowanie stanu maszyn przyczynia się również do zrównoważonego rozwoju. Optymalizacja procesów produkcyjnych i precyzyjne zarządzanie konserwacją redukuje marnotrawstwo zasobów oraz zmniejsza emisję szkodliwych substancji. Przedsiębiorstwa, które wdrażają nowoczesne technologie monitorowania, mogą zwiększyć swoją efektywność energetyczną i zmniejszyć wpływ na środowisko, co jest istotnym elementem współczesnych strategii zrównoważonego rozwoju.
Przewaga konkurencyjna i redukcja ryzyka
Dzięki zaawansowanemu monitorowaniu stanu maszyn, firmy mogą uzyskać znaczącą przewagę konkurencyjną. Minimalizacja ryzyka nagłych awarii i zatrzymań produkcji jest kluczowym czynnikiem sukcesu. Planowanie działań konserwacyjnych na podstawie analizy danych pozwala na zwiększenie efektywności procesów produkcyjnych oraz zapewnienie ciągłości operacji.
Inwestycje w przyszłość
Inwestowanie w nowoczesne technologie monitorowania stanu maszyn to inwestycja w przyszłość przedsiębiorstwa. Firmy, które decydują się na wdrożenie takich rozwiązań, zyskują nie tylko na efektywności operacyjnej, ale również budują swoją reputację jako innowacyjne i zrównoważone organizacje. W dłuższej perspektywie, takie inwestycje przynoszą zwrot w postaci niższych kosztów eksploatacji, mniejszej liczby przestojów oraz większej satysfakcji klientów.
Podsumowanie:
W erze Przemysłu 4.0, nowoczesne podejście do monitorowania stanu maszyn przynosi liczne korzyści. Redukcja liczby użytych czujników, zaawansowane technologie automatyzacji oraz precyzyjna analiza danych umożliwiają skuteczne zarządzanie i konserwację maszyn. Nasza firma, łącząc tradycyjne metody z nowoczesnym podejściem do predictive maintenance, oferuje kompleksowe rozwiązania, które minimalizują ryzyko awarii i zwiększają efektywność procesów produkcyjnych.